Rapid Pressurization Valve
Are you concerned that a fast moving pneumatic component/clamping device could damage your product or workpiece? Are you finding it difficult to control the speed of a clamping device? Ideally, you want the clamping device to move slowly until it reaches the product or workpiece but then you want the pressure to increase rapidly to provide the desired maximum holding force. Perhaps you considered using a fixed orifice. A fixed orifice will slow the movement of the clamping device as desired, however an orifice will also increase the time required, after the clamping device contacts the product, to reach the maximum holding force. This delay needlessly increases the cycle time. Beswick has a solution to this problem.
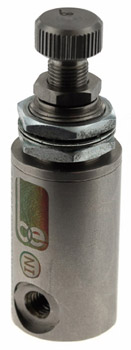
The Beswick Rapid Pressurization Valve (RPV) combines the speed control of a needle valve or a fixed orifice with the rapid, high force holding power of a completely open valve. The RPV functions as a needle valve that opens fully upon sensing back pressure. With an RPV installed in-line with your press, cylinder or actuator, the flow is controlled during free movement allowing your fixture to slowly and safely contact the workpiece for accurate positioning. When the workpiece has been contacted, the RPV opens quickly to provide full clamping force.
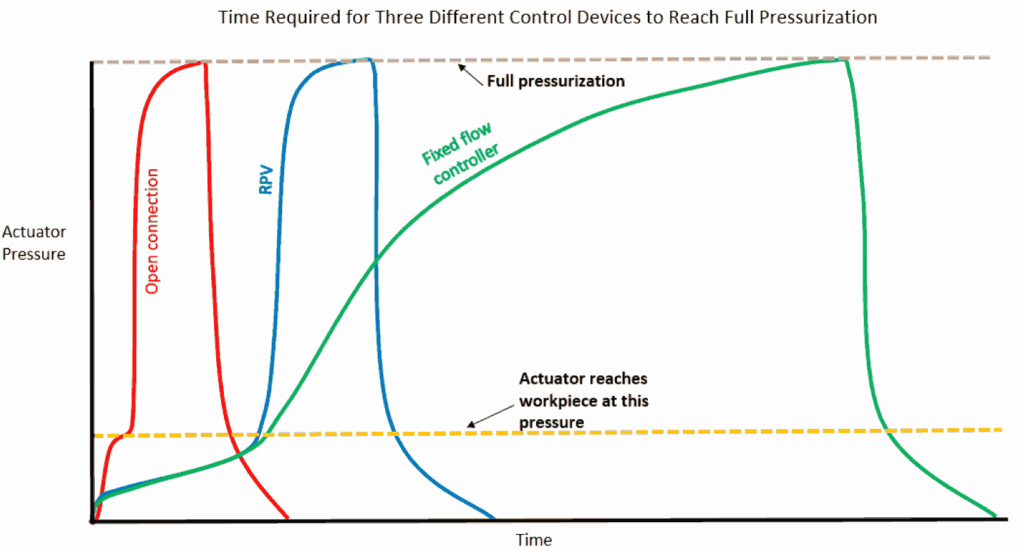
Included Adjustments
The Beswick RPV provides two adjustments that independently control actuation speed and the post contact opening pressure of the valve. The adjustment on the side of the valve controls the actuation speed, while the adjustment screw on top controls the pressure at which the pressure/flow switches from controlled to free flowing.
Side Adjustment: Actuation Speed
This adjustment controls the initial fluid flow rate and therefore the speed of the actuator. The desired actuation speed will depend upon the nature of the equipment involved, so always be sure to adjust your RPV accordingly.
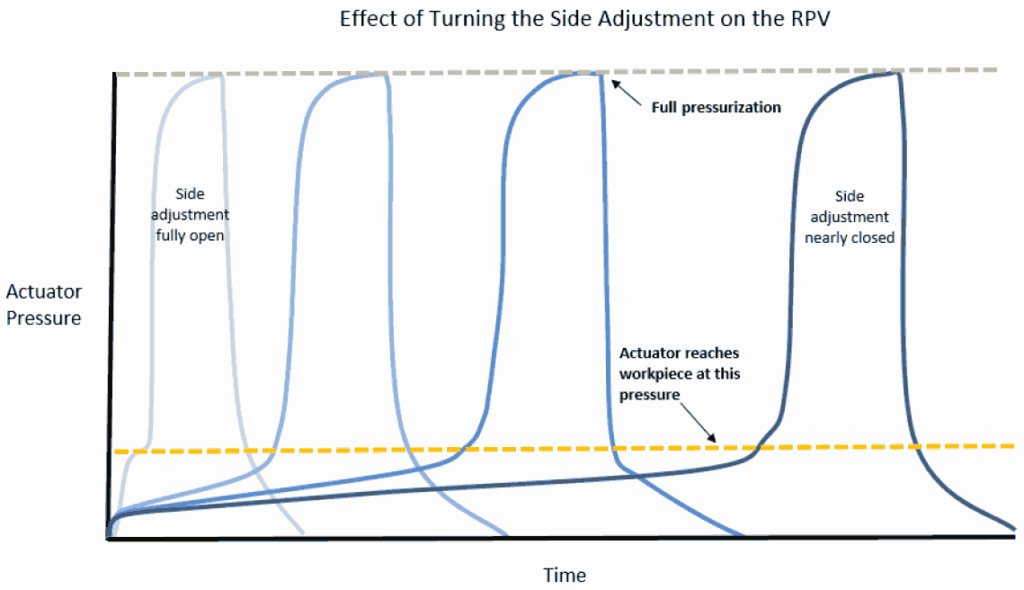
Top Adjustment: Pressure
The adjustment on the top of the valve controls the pressure at which the main valve opens. Conditions may dictate either a low or high opening pressure depending on the application. For the fastest time to full clamping force, set the top adjustment to a low pressure. This allows the RPV to open fully as soon as the actuator has contacted the workpiece for a quick response time.
In applications requiring a slower response time or an additional level of safety, turn the top adjustment knob clockwise until it bottoms out. Then, slowly turn the knob counter clockwise until the main valve opens fully. This method will increase the delay before the inner valve opens and provide an additional level of safety. If the top adjustment is over- tightened, the RPV will act as a fixed orifice, remaining restricted even after your actuator has made contact with your workpiece.
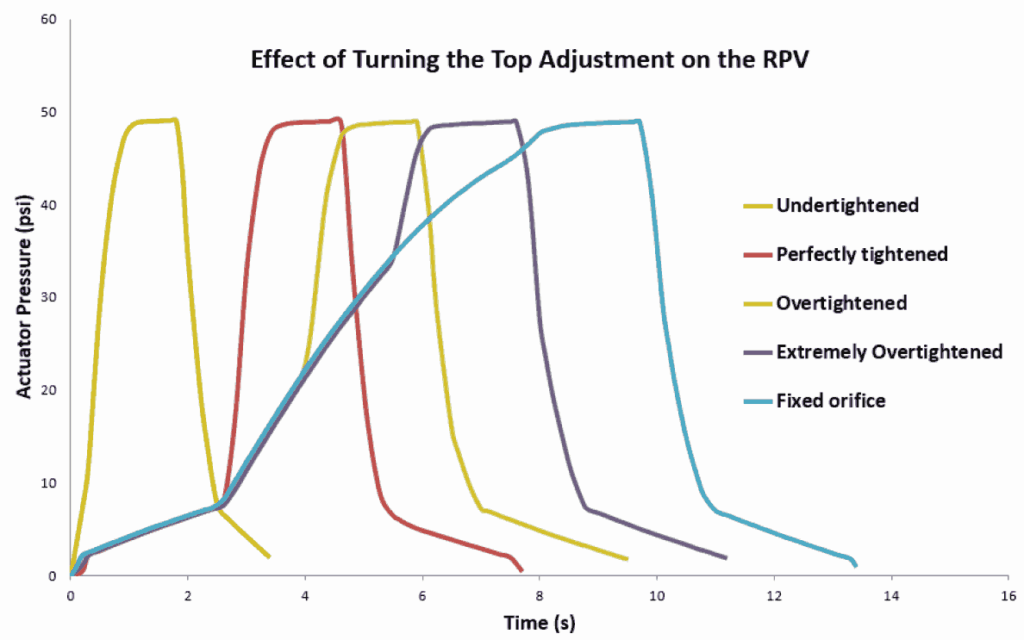
Rapid Pressurization Valve in Operation
The chart below shows the downstream pressure from the RPV as it controls an actuator over the course of its normal operation. The red region is the actuator moving slowly as it approaches the workpiece. At the red-purple intersection the actuator makes contact with the part, and the back pressure begins building. At the purple-yellow intersection, the back pressure becomes high enough to open the main valve to quickly provide full clamping force. In the green region the actuator has reached full pressurization/force. Finally, in the blue region, the actuator is vented and reset for the next part.
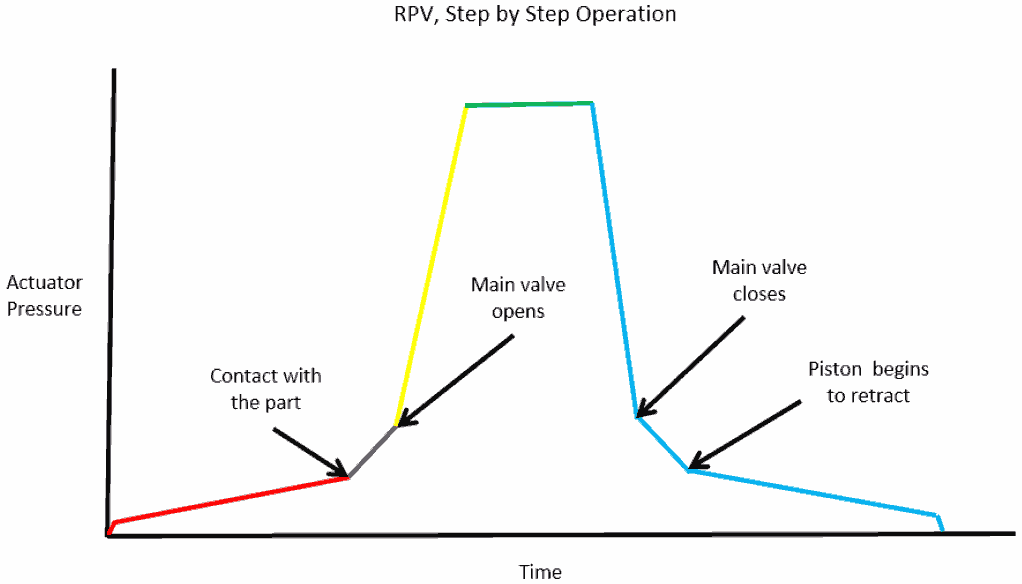
Overall Specifications:
The RPV is designed with 10-32 UNF inlet and outlet ports.
It is 11/16 inch in diameter and about 2 ¼ inches in total length.
The effective orifice (ax maximum opening) is 1/16 inch.
Materials of construction are stainless steel with Buna-N seals.
Weight is approximately 57 grams. Maximum pressure rating is 250 psig.
Summary
The RPV is used to protect a pneumatic actuator such as a chuck, press, or gripper from sudden bursts of high pressure. The internal needle valve restricts the initial movement of the actuator to a user defined speed, and then opens up upon sensing back pressure. This allows the user to limit the impact that a workpiece experiences when it is clamped down upon without sacrificing the pressurization speed of an open, free flowing connection.