This white paper will help you to determine which miniature (barbed, push-to-connect, or compression) fitting type is suitable for your specific application.
At the beginning of a new project, engineers and designers are faced with many important decisions regarding the selection of components. As you would expect, the most complex components are selected first. The selection of relatively simple components, such as fluid power fittings, is often put off until the end of the design cycle. With limited time available to conduct research, even experienced designers and engineers can use help selecting the best type of fittings for their application.
Before a miniature pneumatic fitting is chosen for an application the hose or tubing must be selected. Tubing types commonly found in miniature fluid power applications range from rigid metal (such as copper and stainless steel) to relatively flexible elastomeric or polymer tubing and hose (such as polyurethane, polyethylene, nylon, Teflon®¹, PEEK®², PVC, Silicone, Viton®³, and others).
There are many design considerations when selecting tubing. Chemical compatibility with gas or liquid, minimum and maximum pressures, expected temperature extremes, need for rigid or flexible lines, ease of assembly and maintenance, and external environmental conditions will determine which tubing or hose to specify in the application.
There are three common types of fittings used in miniature fluid power applications:
This table summarizes the fitting selection process. Read on to learn more about the individual fitting styles.
Design Parameters | Barbed Fitting | Compression Fittings | Push to Connect Fittings |
---|---|---|---|
Seals | |||
Fitting Seal on ID | ✔ | ||
Fitting Seal on OD | ✔ | ✔ | |
Pressure Range | |||
Below 125 psi | ✔ | ✔ | ✔ |
Above 125 psi | ✔ | ||
Tubing/Hose Material | |||
Soft Tubing/Hose | ✔ | ✔* | |
Hard Tubing/Hose | ✔ | ✔ | |
Metallic Tubing | ✔ | ✔** |
Note:
*Depending on the duromter (Typically 95 shore A or higher)
**May require tubing modification
Barbed Fittings

The “line contact” barb is the preferred design
On the “line contact” barb fitting, the edge of the barb makes a “line contact”, as opposed to a surface contact, with the tubing wall. In addition, the tubing makes a “surface contact” with the fitting shank. When the fitting is properly designed, the tubing expands over the “line contact” barb and then contracts back onto the fitting shank behind the edge of the barb. The sharp barb digs into the inside diameter of the tubing making a high pressure contact and providing a leaktight seal. Properly designed barbed fittings allow the tubing to be easily pushed onto the fitting but make it difficult to pull off.

“Christmas-tree” (multiple barbs of increasing diameter) barb do not seal as well
This is the “old standard” design and is still found in many industrial applications but has many disadvantages. On first appearance, this design looks like it could hold tubing more securely than a single “line contact” barb. However, the multi-barbs, of progressively larger diameter, may disperse the holding power of the tubing over a greater area. This distribution of force over a large area reduces the holding force and also increases the chance of leakage. Additionally, it is usually more difficult to push tubing onto a fitting designed with progressively larger barbs.
Both types of barbs work best with flexible tubing with excellent memory characteristics, such as polyurethane. The best “line contact” barb designs can withstand the full burst pressure of the tubing without failure. Nevertheless tubing clamps are generally recommended when system pressures approach the 80 to 100+ psi range (depending on the tubing ID, cross section, and durometer). Tubing clamps add reliability and handle pressure pulses and heat issues. Tubing clamps also prevent the internal pressure from lifting the tubing off the barb(s). Barb style fittings take up less space compared to push-to-connect and compression style fittings because barbed style fittings seal on the inside diameter of the tubing. Barbed style fittings are limited to relatively low pressures (usually below 150 or 125 psi) due to the limitations of the soft and flexible tubing. Barb style fittings also have smaller waterways than push-to-connects or compression fittings.
Push-to-Connect Fittings
This type of fitting may be called by several different names depending on the manufacturer. The common feature is that the tubing or hose can be removed from the fitting by pushing on a releasing collar for occasional disconnections/connections. If many disconnection/connection cycles are anticipated a true quick disconnect should be specified instead of a push-to-connect style fitting. In this fitting style, the tubing is held in place by a flexible toothed collet, that bites into the outside diameter of the tubing. The collet teeth are moved away from the outside diameter of the tubing when the releasing collar is depressed and that allows the tubing to be pulled out of the fitting. An o-ring or other type of seal inside the fitting makes a radial seal on the outside diameter of the tubing. Push-to-connect fittings are typically used with higher durometer (95 shore A or higher) tubing materials such nylon, PEEK®, polyurethane (higher durometer versions), and Teflon®. Some special types of push-to-connect fittings are made to work with metallic tubing. In some designs the OD of the metallic tube may need to be grooved to accept the teeth of the collet.

Push-to-connect style fittings have found wide acceptance in most industries because of the ease of connection and disconnection. They are especially convenient when working on a prototype design because of this feature. These style fittings also offer larger waterways than barb style fittings. However, there are some downsides. Push-to-connect fittings take up more space than barbed style fittings because the fitting body must encompass the outside diameter of the tubing. In contrast, barbed style fittings seal on the inside diameter of the tubing so they do not have to be as large as push-to-connect fittings. Another important factor is the reliability of sealing. For the fitting to seal properly, the outside diameter of the tubing must be round and free of scratches. Tubing can be scratched during removal as it slides by the metallic collet teeth. The scratches on the tubing can result in a leak when the tubing is pushed back into the push-to-connect fitting. Lastly, most push-to-connect fittings are recommended, like barbed fittings, for low pressure applications.

Compression Fittings
Compression fittings are a good choice for use with metallic tubing, such as stainless steel and copper, and also hard polymeric elastomeric tubing such as PEEK®, nylon, Teflon®, Kynar®⁴, and polyethylene. Compression fittings are typically used for higher pressure applications (from 150 psi upward) or when the cleanliness and/or temperature resistance of stiff tubing such as stainless steel, PEEK®, Teflon®, or Kynar® is needed.Compression fittings consist of a fitting body, either a one-piece or a two-piece ferrule, and a compression cap or nut. Tightening of the compression cap or nut pushes the ferrule into the tapered angle in the fitting body and thereby compresses the ferrule onto the outside diameter of the tubing. This interference creates the seal and also secures the tubing so it cannot slide out of the fitting. Compression fittings can be disassembled and reassembled but generally only a few times before either the ferrules and/or the fitting body should be replaced to insure a leak-tight seal.
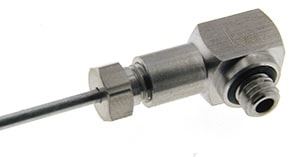
Like push-to-connect fittings, compression fittings are bigger than barbed style fittings because they seal on the outside diameter of the tubing. Compression fittings are more reliable than push-to-connect fittings and can take much higher pressures but are not as convenient in terms of connection and disconnection.
Compression fittings do not work well with softer tubing because the tubing must resist the compression of the ferrule. Some fitting manufacturers offer metallic tubing supports that can be inserted into the inside diameter of softer tubing materials to insure that the tubing does not collapse when the ferrule is swaged into the outside diameter of the tubing.
Many customers use Teflon® tubing with compression fittings since it is resistant to most chemicals and will handle relatively high pressures. A disadvantage of Teflon® is its propensity to “cold flow”. Teflon® will tend to move away from an applied load (such as a compression ferrule) over a period of time. High heat can increase this problem.
Threads
Common Metric and English Sizes – Straight Fittings
You must know the specifications of the threaded port you will be installing the fitting into so that you can select the appropriate fitting. Miniature fittings come in many thread sizes. Some of the most common are: M3 x 0.5, M5 x 0.8, M6 x 1, and M8 x 1.25 in metric sizes and 10-32 UNF, ¼-28 UNF, and 5/16-24 UNF in unified screw thread sizes. These are straight threads (not tapered like pipe threads). A seal, usually an o-ring or gasket is required to prevent leakage from straight threaded fittings.
Pipe Thread Sizes
Tapered pipe threads, such as 1/16 – 27, 1/8 – 27 and ¼ – 18 NPT, are also very common since they have been used for so many years. Tapered pipe threads are somewhat vibration resistant. They are in widespread use throughout the industry and in HVAC type plumbing but tapered threads have disadvantages. Pipe threads leak unless a thread sealant is used. Additionally, due to the tapered thread design, pipe threads do not allow for an easy way to position the outlet of elbow and tee fitting configurations. The only way to position the outlet(s) is to vary how much the fitting is tightened or loosened and that can lead to over tightening or leakage.
Seals
O-ring versus Gasket Seal
In the past, flat soft elastomer, hard plastic, or metal gaskets were used to seal straight threaded fittings. This sealing method presented a number of problems including assembly issues, leakage, and loose fittings. A far superior sealing method is to use a captured o-ring face seal. This sealing method eliminates leaks, compensates for rough surface finishes in mating parts, provides greater installation torque (secure connection), eliminates the need for thread sealants, and greatly reduced assembly time. Numerous o-ring elastomers are available to handle a wide range of temperatures and chemicals.